Activities in the Development Stage
In the development stage, we design our vehicles to avoid using environmentally harmful substances in their construction and make them easier to recycle. Additionally, to reduce our use of nonrenewable resources, we give consideration to the use of recycled plastics, other recycled materials, and renewable bio-materials. We are also examining the possibility of recycling plastic parts from end-of-life vehicles and using this material for new vehicles, searching for ways to overcome the technical challenge of maintaining quality.
3R design activities
- Design and resource reduction
Considering the recycling of end-of-life vehicles and reuse of parts, it is important that design be conducted with consideration of the 3Rs (reduce, reuse, recycle) during new vehicle development. We therefore prepared Design Guidelines to advance recycling design of new vehicles. These guidelines suggest areas for improvement and new ideas for design with consideration for the 3Rs.
- Recycling ease (recoverability rate)
- Ease of dismantling at the end-of-life stage (dismantling efficiency)
- Material identification markings for plastic parts (plastic part marking)
- Reduction of environment-impacting substances
Development process for 3R* design
- Design and resource reduction
Nissan received ISO 14001 certification for its product development process in fiscal 1998.
We have established targets for the recoverability rate, dismantling efficiency, plastic part marking, and reduction rate for environment-impacting substances in the development of new vehicles. We have also set clear criteria for the design stage, and are conducting management and evaluations of our progress in achieving these targets.
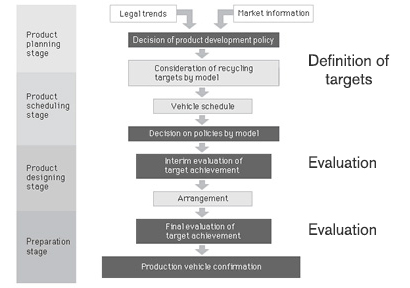
Reduction of environment-impacting substances
- Design and resource reduction
Stricter controls on the environmental impact of substances are being implemented in countries around the world. Examples include the European ELV Directive and the European Commission's Registration, Evaluation, Authorization and Restriction of Chemicals (REACH) Regulation, which went into force in June 2007. To help minimize the potential release of formaldehyde, toluene and other volatile organic compounds (VOCs) in vehicle cabins, the Japan Automobile Manufacturers Association has launched a voluntary program that calls for all new models launched in Japan from April 2007 to meet standards set by the Japanese Ministry of Health, Labor and Welfare for concentration levels of 13 compounds in vehicle interiors.
Nissan outlined a globally uniform policy in 2007 on reducing the use of environmental-impact substances, strengthening the management of such substances, adhering to a well-planned schedule for their reduction and advancing the use of alternative substances. Based on this policy, we have developed the Nissan Engineering Standard for the "Restricted Use of Substances." The standards identify the chemical substances whose use is either prohibited or controlled, and they are applied in selecting the materials, components and parts used in Nissan vehicles from the stage of initial development. For example, the use of four heavy metal compounds (mercury, lead, cadmium and hexavalent chromium) and the polybrominated diphenyl ether (PBDE) flame retardant has been either prohibited or restricted in all new vehicles (excluding OEM vehicles) launched globally since July 2007.
With Renault, we have strengthened our alliance efforts by implementing common standards for reviewing hazard and risk selection standards exceeding legal compliance levels. Nissan, together with its suppliers, builds and operates information transmission and management mechanisms both internally and in the supply chain. For example, for cars and parts produced or imported into Europe, we provide information, register and notify government agencies to comply with the REACH and CLP (Classification, Labelling and Packaging of Substances and Mixture) regulations.
Reducing Scarce Resource Usage
- Design and resource reduction
With electrification, many components will require larger quantities of scarce resources such as rare earths. Uneven distribution of rare earth elements and the forces of demand and supply give rise to concern about price changes, so minimizing their usage is an important question to address.
In 2012, Nissan has developed in a joint effort with our supplier, a new electric motor that reduced the use of dysprosium (Dy), a rare earth element, by 40 percent compared to conventional EV motors. The new, more environmentally-friendly motor started being used in an updated version of the Nissan LEAF, released in Japan in November 2012.
Since their adoption in the Nissan LEAF, we have continuously reduced heavy rare earth elements in motors for electric motor-driven vehicles. In 2020, the Note e-POWER adopted magnets with 85% less heavy rare earth elements compared to 2010.
Furthermore, the 2022 Nissan ARIYA has a magnet-free EV motor, which does not contain Dy at all.
Dysprosium-saving technology (grain boundary diffusion technology)
Previously, dysprosium was added uniformly throughout the neodymium magnet. The newly developed motor adopts a “grain boundary diffusion technology”, making it possible to reduce the amount of dysprosium used by 40% while maintaining the same heat resistance as before. In order to increase the heat resistance of neodymium magnets, it is effective to distribute dysprosium at the crystal grain boundaries (crystal boundaries) of the magnets. Grain boundary diffusion is a technology that builds on these characteristics and keeps heat-resistance levels comparable with conventional electric motors.
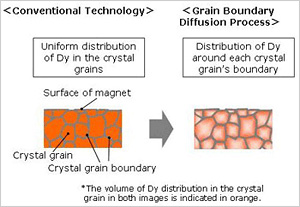
Expanding our closed-Loop recycling system
- Recycling
“Closed-loop recycling” is a way of recycling waste products generated during production, scraps, and in-house used products, while maintaining the quality of the materials so that they can be reused as components of the company's products. This approach allows the same materials to be used repeatedly, greatly reducing CO2 emissions and environmental impact during the product life cycle.
Nissan, in particular, focuses on three types of components which make up a high proportion of the materials used to build cars, and have relatively high environmental impact (mining natural resources, energy use during processing and disposal): “steel”, “aluminum” and “plastics”.
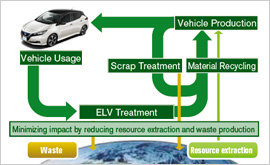
Closed-Loop Recycling
Steel and aluminum
- Recycling
In addition to efforts to reduce steel scraps generated during production, we are working to collect scraps generated in cooperation with business partners in order to recycle and convert them into automotive materials.
We are promoting the collection and recycling of used aluminum road wheels.
Aluminum wheel recycling
Nissan has made it possible to recycle aluminum road wheels at Nissan’s factories recovered from end-of-life vehicles for use in high-quality suspension parts. This reduces the use of virgin materials. Conventionally, waste aluminum materials have been widely recycled as aluminum parts, including engines, but a higher grade has been achieved by thoroughly collecting only Nissan's aluminum road wheels at recyclers all over Japan.
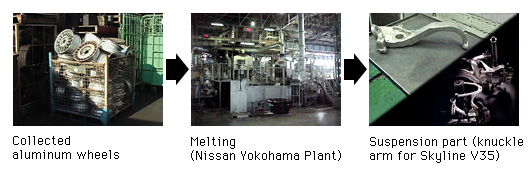
Plastics
- Recycling
Painted bumper scrap generated at the manufacturing sites is recycled at the Oppama factory by removing the paint film in a bumper regeneration process. These have been reborn as bumpers for new cars and are used in many models, including the Nissan LEAF. Bumpers exchanged at dealers are collected and usually recycled as materials for components such as undercovers, etc.
Development of technology to recycle removed bumpers
We developed a device that crushes the bumpers collected by Nissan and removes the paint film at a lower cost and without using chemicals. In this way, we are able to reuse this material, which will firstly be used as a component of repair bumpers, and in the future for new car bumpers.
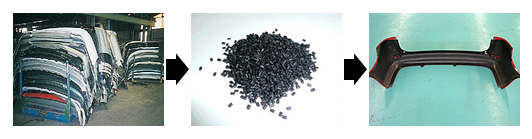
Development of new recycling technologies
- Recycling
Nissan is actively working on the development of new recycling technologies with the aim of expanding the scope of recycled materials, and reducing the need for virgin materials through advanced recycling technologies. In order to contribute with the aim to reduce the dependency on new natural resources, as stated in the long-term vision of the Nissan Green Program, further advancement of recycling technologies is essential. We believe that these efforts will be necessary not only for Nissan, but also for society as a whole. Nissan is implementing advanced recycling projects, including (1) Shredder dust recycling technology, (2) Lightweight car body recycling technology, (3) Electric unit recycling technology, and (4) Plastic workplace partition recycling technology. (Latest results available at: (Japanese only))
1.Shredder dust recycling technology
About 200 kg of shredder dust is generated per vehicle when recycling used cars. About 30% of shredder dust is mixed plastics, and only about 0.5% of automotive shredder dust (ASR) is currently recycled. In order to reduce ASR generation, advanced sorting of mixed plastics contained in the shredder dust material is necessary. Based on the properties of the components, material recycling and chemical recycling process is being developed in order to allow for these materials to be recycled as automotive materials.
Case) Optimization of recycling process for plastics recovered from ASR
Based on its specific properties, we developed a process for selectively recovering high-quality propylene (PP) from the mixed plastics in the ASR, as PP is the plastic used in the highest amounts in cars. We developed this technology with Veolia Genetz Co., Ltd. and related companies. Based on the results obtained, we are further advancing our technology to soon apply it to automotive parts.
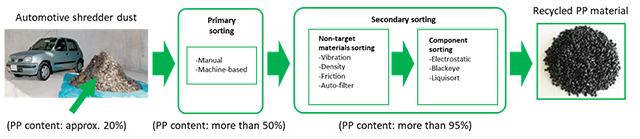
2.Development of recycling technology towards lighter car bodies
The use of lightweight materials such as aluminum panels and CFRP is expected to increase in the future. By further reducing car body weight, the resulting improvement in fuel efficiency will reduce CO2 emissions while driving. These lightweight materials have high performance and functionality, and when end-of-life vehicles enter a recycling stream, it is desirable to perform closed-loop recycling and maintain material value.
Case) Development of advanced sorting technology for automotive aluminum panels
Aluminum panels are available in multiple alloy grades based on the required properties for each application. In order to collect aluminum panels from used automobiles and recycle them as closed-loop aluminum panels, sorting by alloy grade is essential. LIBS (Laser Induced Breakdown Spectroscopy), though attracting attention as a high-level sorting technology for alloy components, has application difficulties for metal materials that have been painted over the entire surface, such as automobile body panels. This is due to the fact that the laser is prevented from irradiating the base metal, and does not allow the sorting accuracy to improve. Nissan Motor Co., Ltd. is working with Matec Corporation on the construction of a sorting process for painted aluminum panel scrap by optimizing the shredding method suitable for advanced sorting by LIBS.
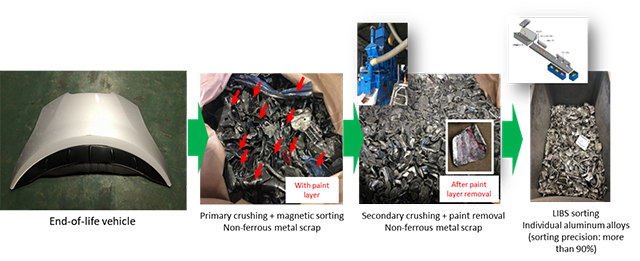
3.Development of recycling technology for electric units
The expansion of hybrid vehicles and electric vehicles (EVs) in the market will contribute to the reduction CO2 emissions while driving. Many rare resources such as rare earths are used for lithium-ion batteries and motors used in these vehicles, and in order to achieve both CO2 reduction and new natural resource usage reduction, it is very important to promote recycling activities.
Case) Rare earth recovery technology development from drive motor magnets
Electric motor (EV) drive motors use neodymium magnets that contain large amounts of rare earths. In addition to reducing the amount of rare earths used, it is important to develop processes to collect rare earths from used motors. In collaboration with Waseda University, Nissan is working on the development of rare earth recovery technology using a dry recycling method using borax (Na2B4O7) as a flux with the aim of reaching high recovery rates.
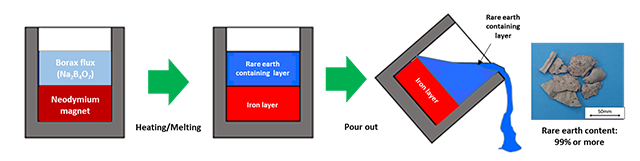
4.Recycling plastic workplace partitions
Nissan is working with material manufacturers and parts manufacturers on a new initiative to recycle plastic workplace partitions that were used at its various facilities. Typically, such used partitions are incinerated as waste. However, to reduce environmental impact, departments such as material technology, design, HR and general affairs, have worked together to develop a way of recycling them into automotive components.
The partitions used at Nissan are made of one of two materials: acrylic called polymethyl methacrylate (PMMA) or polyethylene terephthalate (PET), both of which are recyclable. By recycling them into automotive components, we aim to reduce CO2 emissions, thereby lowering environmental impact.
Example: Recycling into headlamp inner lenses
Acrylic is used to make headlamp inner lenses for cars. Nissan, with Sumitomo Chemical Co., Ltd. and Koito Manufacturing Co., Ltd., chemically decomposes partitions made of acrylic, returning them into raw materials. To manufacture parts, we employed a mass balance approach* that allows for the mixing of recycled materials in the traditional material production line, enabling manufacturing with the Nissan-required quality and precision. We will gradually adopt materials that have reduced CO2 emissions using this technology in the headlamps of the Nissan X-Trail.
- Allocates environmental value based on the amount of recycled raw materials introduced into the production line.
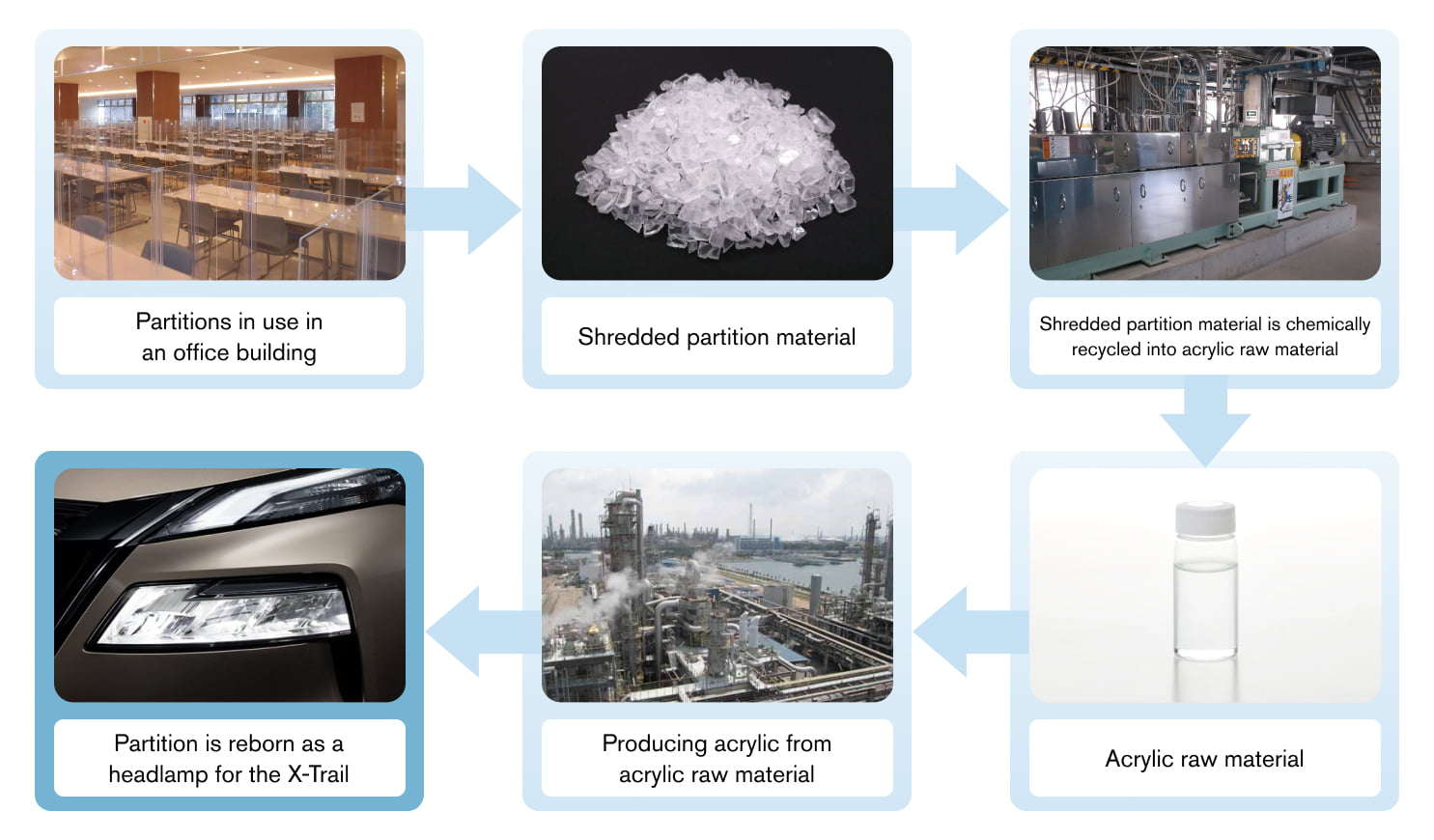
Example: Recycling into roof trims
PET is used in bottles and textile fibers, and in automotive parts such as seats, carpets, and roof trims. Nissan has developed a mechanical recycling technology to manufacture parts with the same quality and accuracy as conventional materials collaborated with Takayasu Co., Ltd., Oyama Chemical Co., Ltd., Japan Vilene Co., Ltd., and Howa Co., Ltd. The resulting materials will be progressively adopted in the roof trims of the Serena.
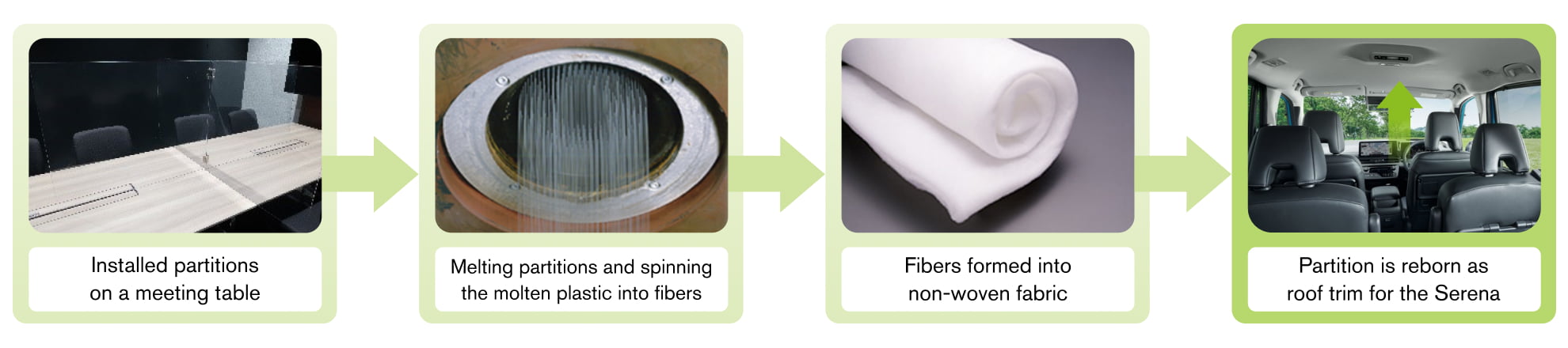
In the future, Nissan will recycle plastic components from end-of-life vehicles, aiming to enhance resource circulation. The recycling involves various processes ranging from collection and crushing/washing to commercialization, posing challenges related to securing the appropriate quality levels and logistics. We will leverage the various insights to promote closed-loop recycling of plastics aimed at reducing CO2 emissions and expanding sustainable materials.