When you think of a factory, various images and associations probably come to mind. Factories have a reputation as grimy, noisy, and perhaps strenuous places to work. At Nissan, we’re out to change those perceptions.
We aim to safeguard both the natural environment and our employees. Worker safety is the prime consideration at our production facilities, with the goal being to create the most comfortable workspace possible.
As we continue to transform our cars and our technologies, we’re taking ever bigger strides to ensure we do the same in our factories. It is necessary that we transform every production line and process in our drive towards a sustainable future.
Our Tochigi Plant has recently gone through a major transformation. The changes to the casting line for cylinder-heads have been particularly marked. It’s now a line where 20% of our staff are female.
Why the casting process?
Located in Kawachi in Tochigi Prefecture, Nissan’s Tochigi Plant boasts a long history of producing the company’s most prestigious vehicles – for example, the GT-R and the Z. As the first Nissan Intelligent Factory, it features a more comfortable and technology-focused production system that is at the very forefront of automotive manufacturing.
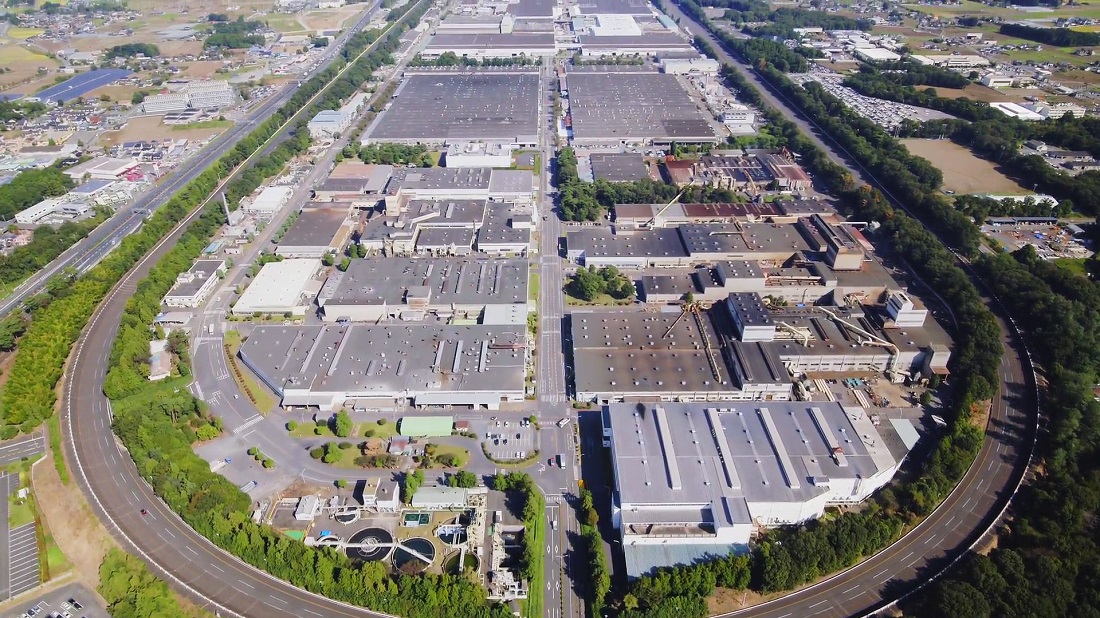
The casting division covers approximately one quarter of the whole Tochigi Plant. This is where we operate the entire casting process – the melting and molding of metals such as aluminum and iron into engine parts.
As at any factory, the foundry and casting processes are inherently some of the most demanding. The processes require extra care to ensure that their environmental impact remains minimal.
For Nissan, this is an area of particular focus.
Creating an even safer working environment
Shinichi Tsuchiya, casting line designer at the Tochigi Plant, explains the approach: "When the factory line renovation project began in 2018, we worked to make the line environmentally friendly and open to all, irrespective of age and gender. That includes those who have difficulties doing heavy work."
Meeting this goal called for a complete overhaul, including the introduction of the latest and most advanced equipment. This allowed the casting department to become both more environmentally safe as well as people-friendly.
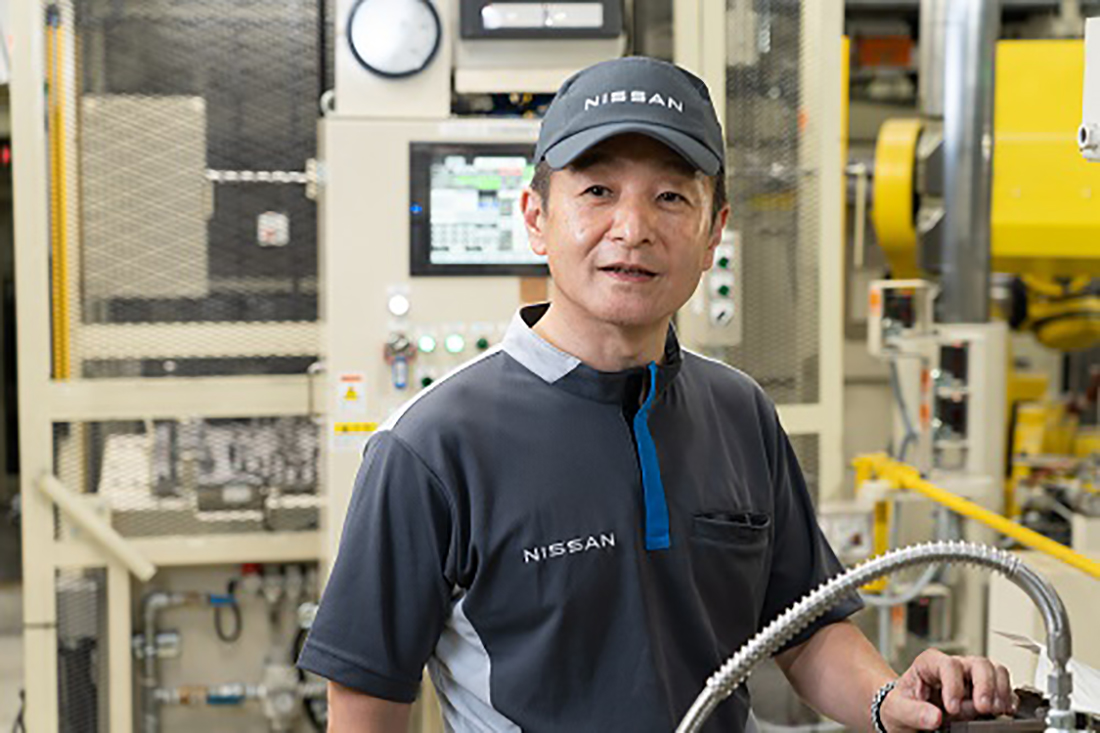
Shinichi Tsuchiya, casting line designer
Bright and uplifting surroundings
Upon setting foot in the new factory, visitors immediately notice the brightly colored floors and well-lit workspaces, which make use of environmentally friendly LED lighting.
The air and overall environment inside the large production facility remain clean thanks to inorganic cores in the casting and molding processes. The organic cores used previously contained an adhesive that, melting during the heating process, would release gasses with a strong and unpleasant odor. We were required to fit deodorization equipment above the molds to tackle this issue.
Now, the inorganic cores we use contain an adhesive called water glass. When melted, this substance generates no unpleasant gasses or odors, eliminating the need for deodorization equipment.
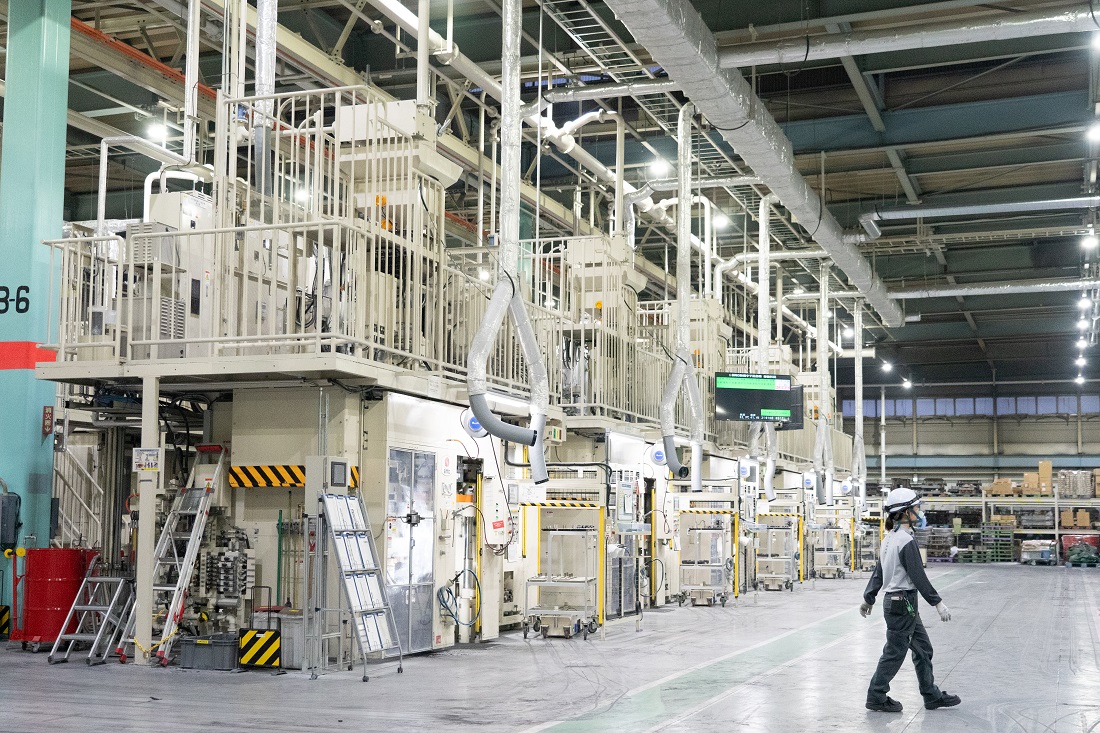
Production area improved via shift to use of inorganic cores
New machinery helps carry the load
We’ve made significant improvements when it comes to reducing the physical strain placed on our workers.
In the past, we transported molten aluminum from the foundry to the casting line by forklift. However, by moving the melting furnace close to the casting machines, there’s no longer the need to transport the molten metal. Furthermore, we’ve reduced energy consumption by melting only the necessary amount, making for a far more efficient process overall.
We’ve also greatly simplified the post-casting inspection process. In the past, the process was extremely intensive. It required the insertion of an endoscope into the cylinder heads so that we could visually check if any broken cores or sand remained inside. Now, we use computed tomography (CT scanning) for a far quicker and more efficient internal assessment. This greatly reduces the workload involved in the process, including the physical burden placed on our people. Previously, we would manually invert the 10 kg cylinder heads for outer inspection. Now, however, the process uses automated rotating machinery and is much easier to manage physically.
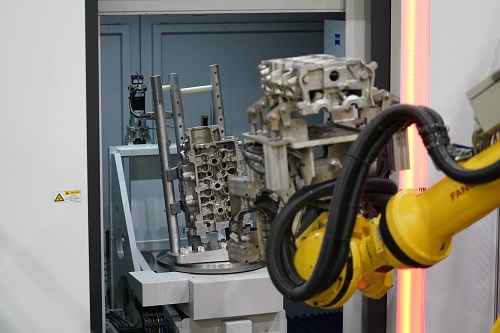
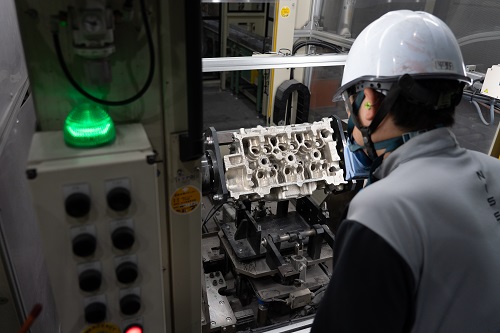
Cylinder head inspection using CT scanning and automated rotating device
Nissan’s continuing drive toward carbon neutrality
Curbing the overall environmental impact of our factories continues to be a major goal. The high-temperature processing previously associated with casting meant that this was one area in which we felt we could effectively reduce emissions. We achieved that goal with a 40% reduction across the heating process.
The heat-treatment process, which saw the biggest reduction of CO2 emissions, is the point at which we strengthen the cylinder heads after molding. The conventional method, in which multiple cylinder heads are placed in a basket and fed into a heat treatment furnace, generated a great deal of heat. However, by changing to a single feed rotary heat treatment furnace, we greatly increased efficiency in this process too.
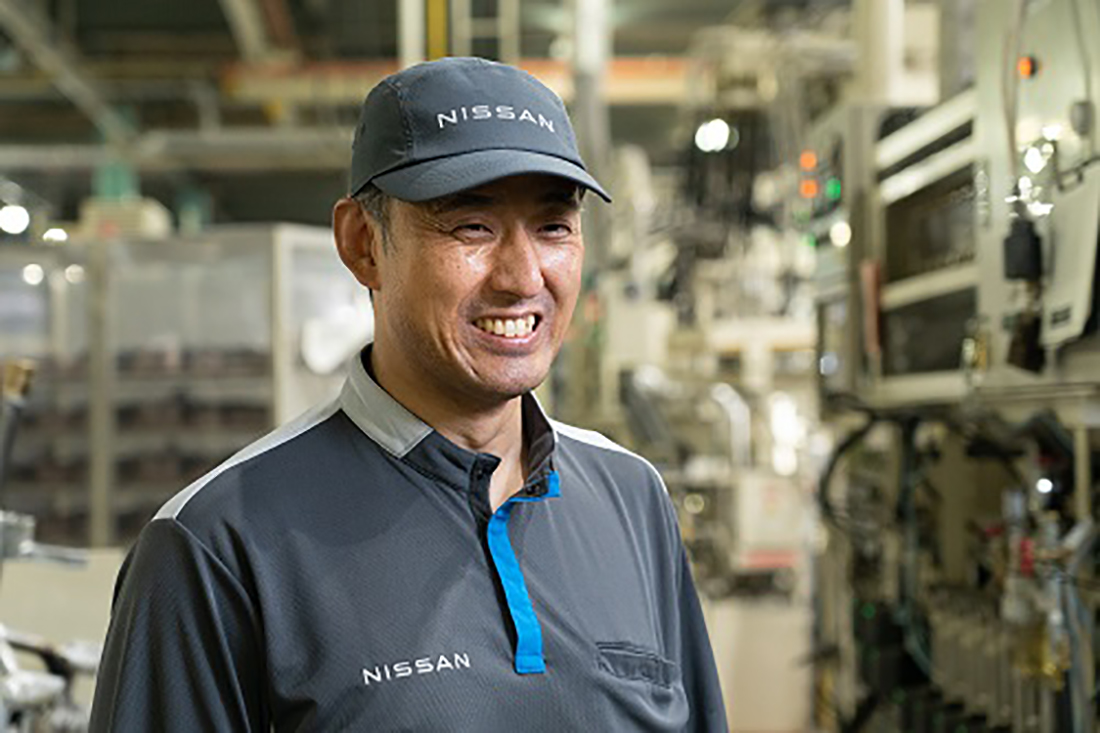
New rotary heat treatment furnace
Benefits felt throughout the casting line team
"The Tochigi Plant has the ability to tackle issues across divisions and processes," says Casting Engineer Yosuke Nagamori. “The strong team ethic has contributed greatly to this improvement.”
Kana Tsugawa, a casting line worker, smiled as she told us that there's now a lot less grime and odor. “The factory’s brighter, and the job is physically easier.” With the reduction of pungent gas emissions, she tells us, the team can now socialize after work without needing to go home to get changed.
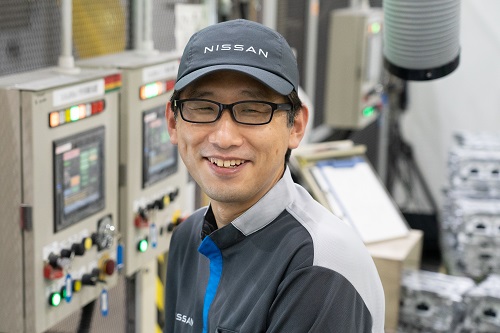
Yosuke Nagamori, casting engineer
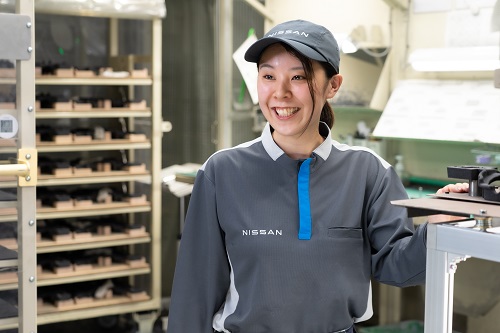
Kana Tsugawa, casting line worker
Ever improving efficiency
Nissan has set the goal of achieving carbon neutrality throughout the vehicle lifecycle* by 2050. The introduction of the Nissan Intelligent Factory at the Tochigi Plant is an important pillar in this initiative. We are promoting innovation of this kind to improve production efficiency in vehicle assembly, both in terms of the energy we use and materials.
As Casting Line Manager Takahiro Nishi says, "We’re excited about the future and remain as proud as ever of our people. Our factory will only continue to transform.”
*Vehicle lifecycle includes the extraction of raw materials, production, use of vehicles, and recycling and reuse of end-of-life vehicles.
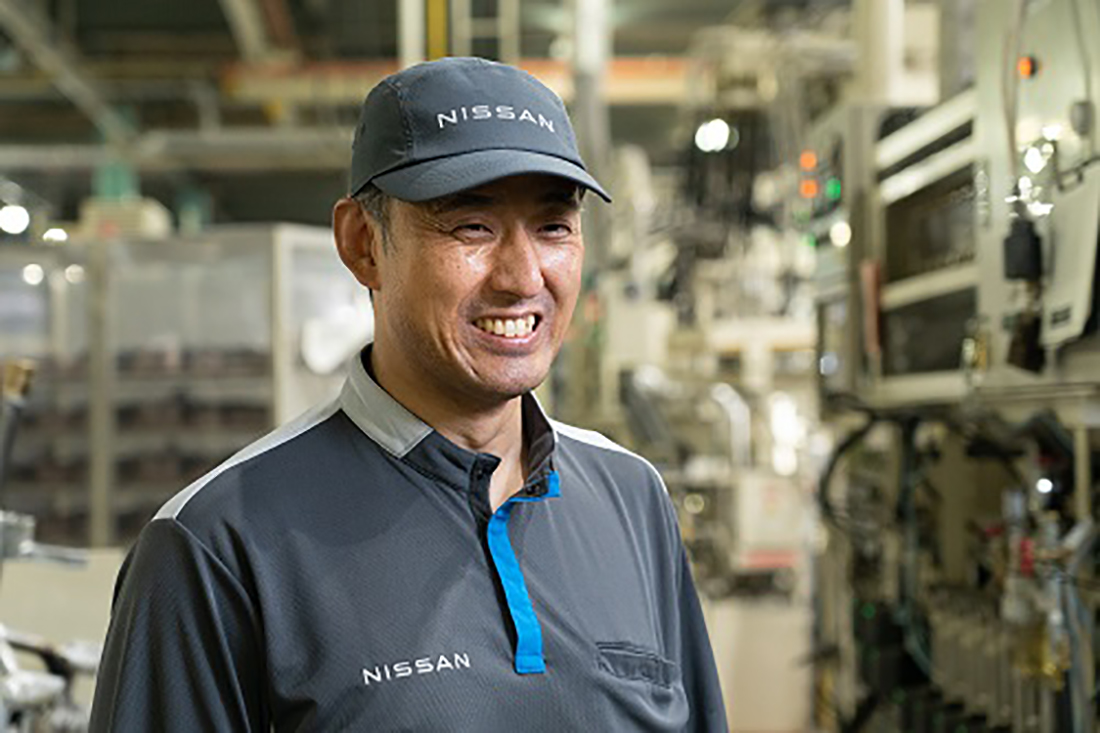
Takahiro Nishi, casting line manager
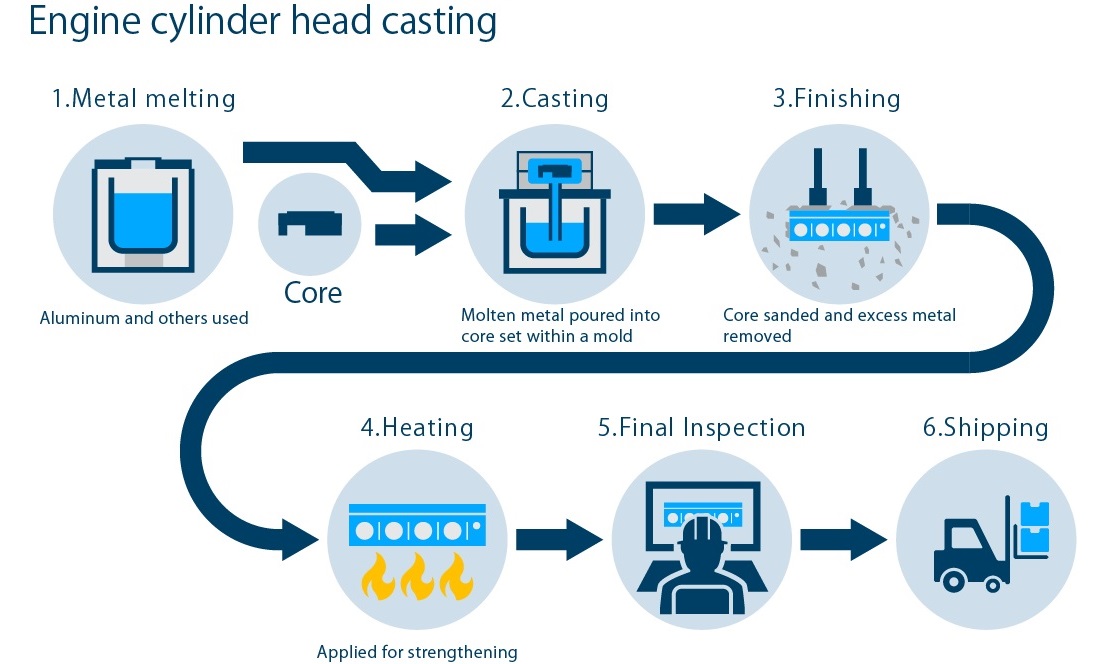