For nearly as long as there have been cars, people have been collecting and customizing them. Until recently, however, if classic-car aficionados wanted to replace a damaged hood or fender on an out-of-production vehicle, they had to hire a craftsman to make a replacement or trudge through junkyards. Now, thanks to a new technology called dual-sided dieless forming, Nissan plans to offer original specification pieces at mass-production prices.
Automakers traditionally form body parts by pressing sheet metal against specially created dies. Designing and building multiple dies for each part is expensive and only pays off after stamping a large volume of parts. This basic process has remained largely unchanged since the early days of mass automaking. It remains a stumbling block that prevents low-volume production of inexpensive parts.
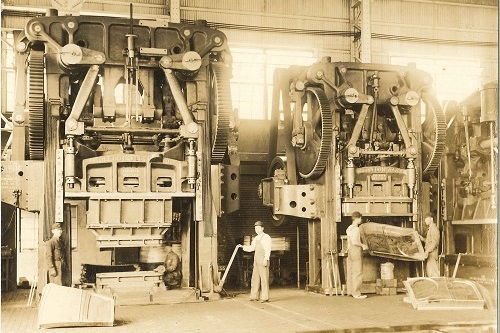
Nissan’s Yokohama (Japan) plant, 1935
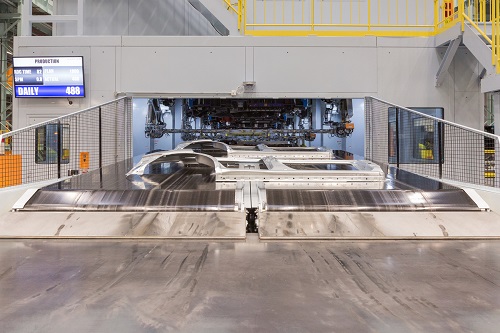
Nissan’s Sunderland (UK) plant, 2017
Nissan’s new dual-sided dieless forming technology presents a compelling alternative to the investment-intensive industry norm. It does away with dies and stamping machines altogether, removing one of the most costly and time-consuming steps in auto body manufacturing.
Two robots are better than one
The process involves two robots working on opposite sides of a flat sheet of metal. By syncing their movements precisely and using diamond-tipped tools developed by Nissan, the robots can shape the metal to a high degree of accuracy and detail. Working in tandem, two robots can produce intricate concave and convex shapes that could not be created if one robot were working from a single side of the sheet.
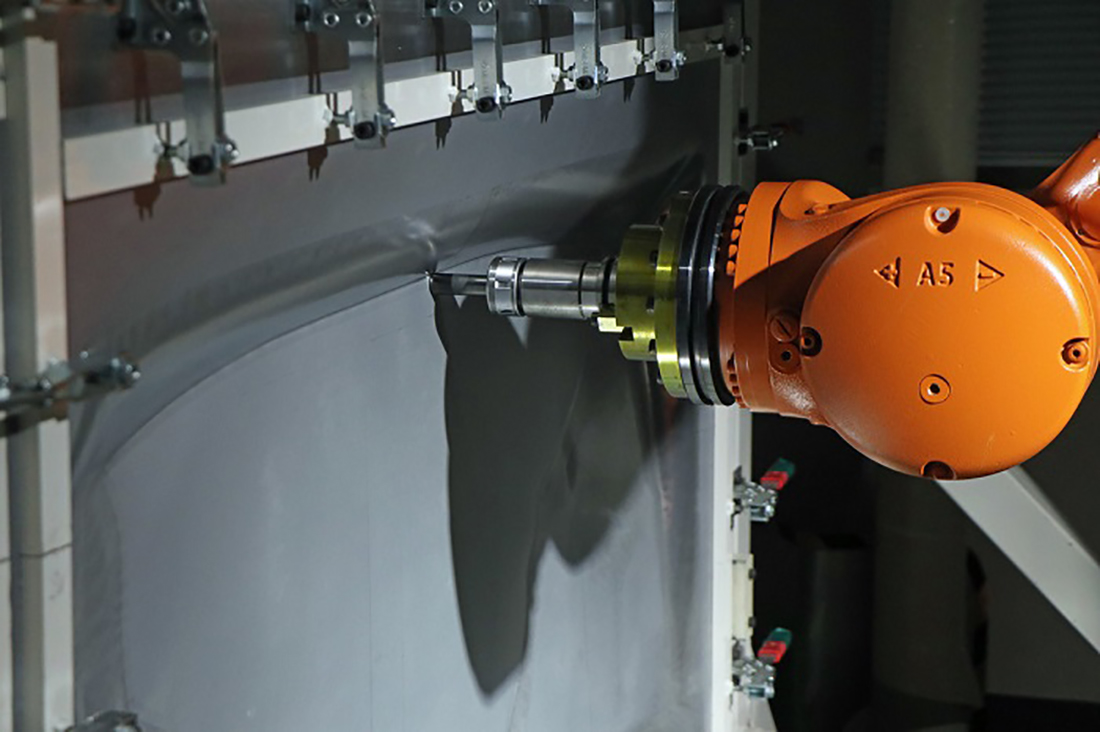
“About five years ago, we started thinking about ways of forming sheet metal without relying on dies,” said Keigo Oyamada, an assistant manager in Nissan’s vehicle manufacturing element engineering department, who oversaw the project. “Our goal was to solve the cost issues related to creating dies for small-volume production. We want to put this technology to use to create spare parts for old models whose dies have already been thrown out, or potentially even to let people order custom parts from Nissan.”
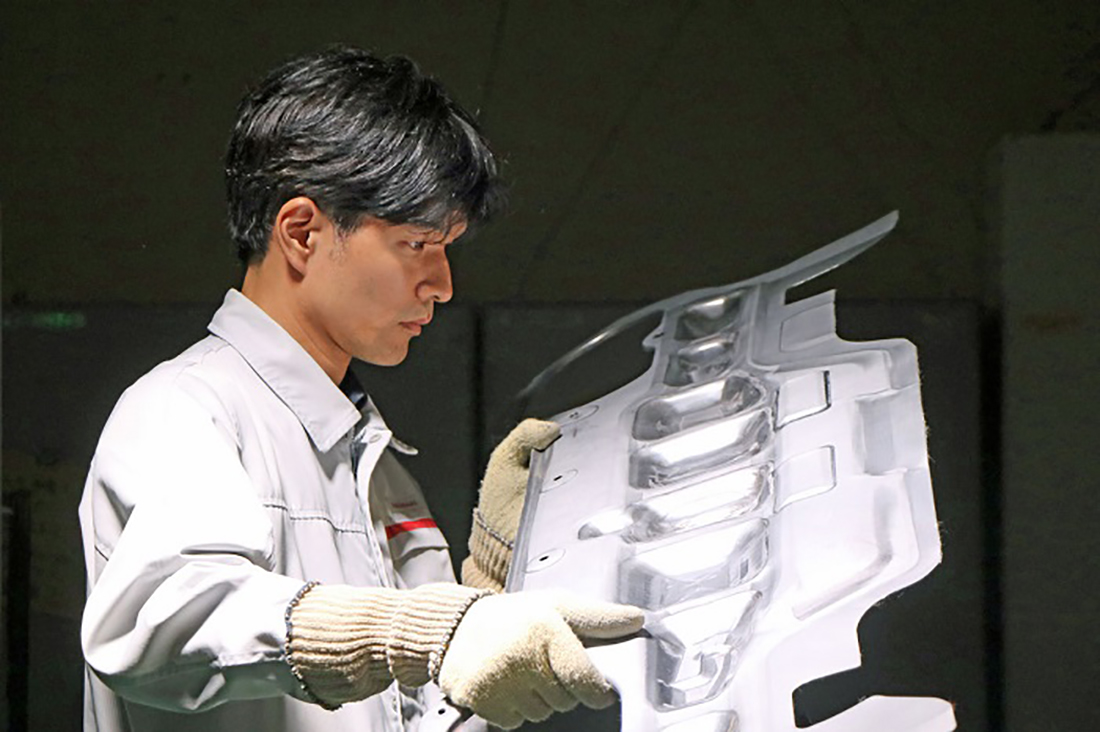
Performing a 3D scan of an existing part creates data that can be used to “teach” the robots to build the scanned part — although some human guidance is still required. This approach will allow Nissan to produce parts that haven’t been made in decades, simply by scanning existing examples of those parts.
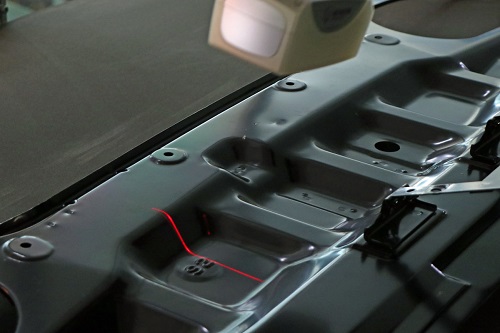
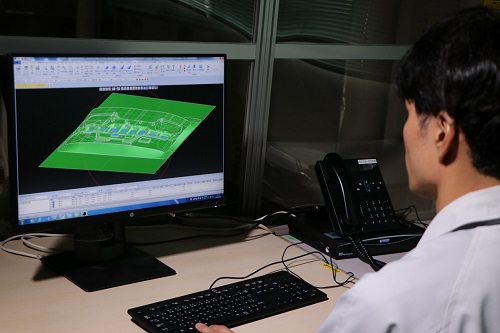
Custom parts – in just one week
Dual-sided dieless forming can be used to create custom body parts in less than a week, instead of waiting as long as a year for dies to be designed and manufactured. The process is also inherently adaptable, and can be used to produce small and large parts alike, as well as car parts other than body panels.
For now, Nissan plans to use dual-sided dieless forming to produce replacement parts for cars the company no longer sells. Looking further ahead, the company sees potential for creating customized parts for those who are looking to add a little uniqueness to their future rides.
To learn more about dual-sided dieless forming, watch the video below or take a look at our announcement last month.
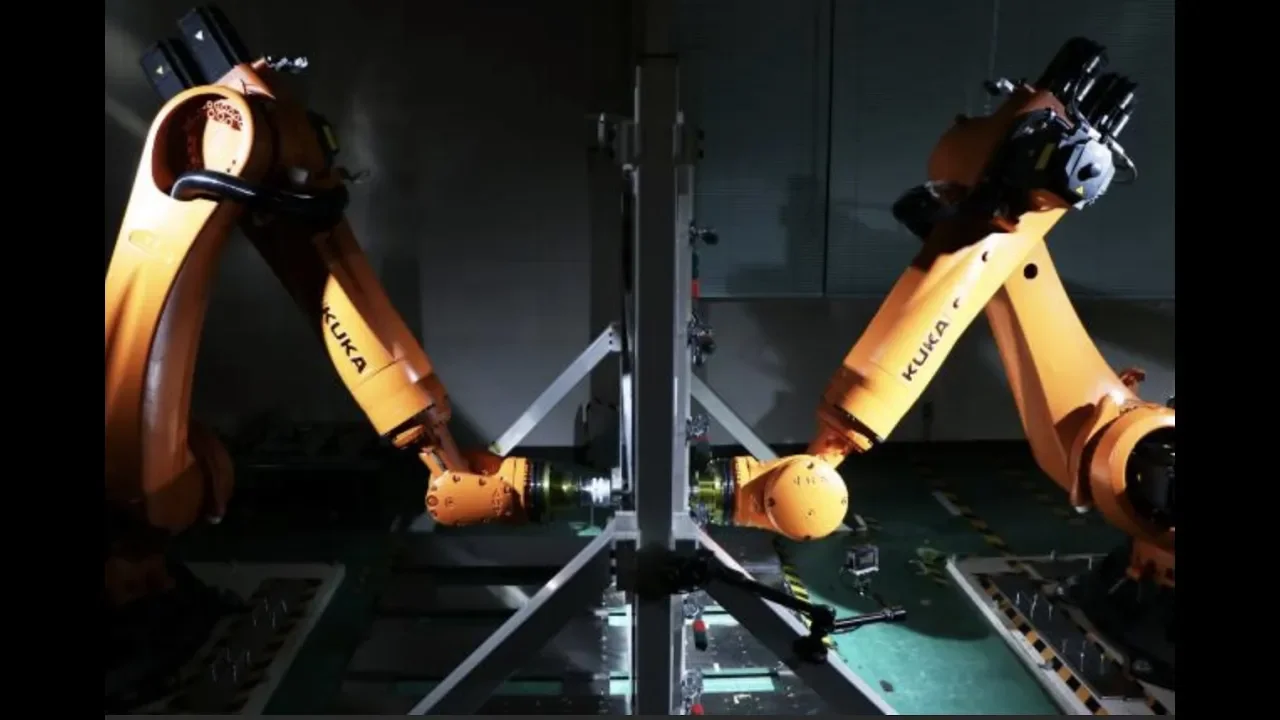