“TAKUMI”Project
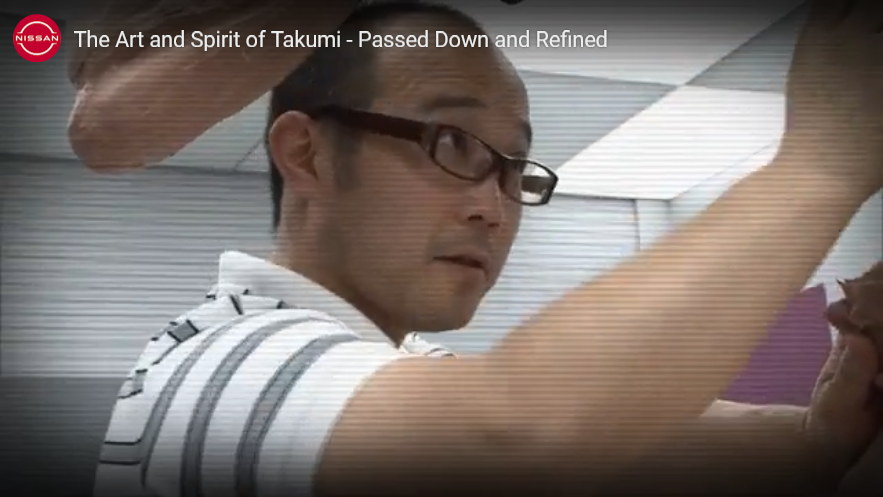
The Art and Spirit of Takumi - Passed Down and Refined1:45
Passing Down Nissan's Skills and Spirit
Clay models are an integral part of the automobile development process. The clay modelers who make them are tasked with understanding the designer's intent and creating models to exact specifications. They must constantly work to hone their skills and their sensibility for the craft. For many years now, Nissan has carried out a project to let them push their talents as far as they can go.
A Project to Help Modelers Grow
Clay modelers take the two-dimensional sketches provided by designers and turn them into three-dimensional models of a vehicle's interior and exterior with a special type of industrial-use clay. As they create their models, they must also ensure that the vehicles will meet legal specifications and remain clear of the constraints of the manufacturing process.
The job is a demanding one, requiring the modelers to be fully equipped with both the sensitivity and imagination to perceive just what the designers have in mind and the expressive techniques to turn those designs into real objects.
For more than 20 years now, Nissan's Global Design Center has run the Takumi Project to help clay modelers improve their design sense and modeling skills. Participants leave their usual workplaces behind for several months to join others from different teams in crafting clay models unlike any they have worked on before.The most recent Takumi session brought together seven modelers, including everyone from young workers who had joined Nissan just a few years earlier to veterans with more than three decades under their belts.
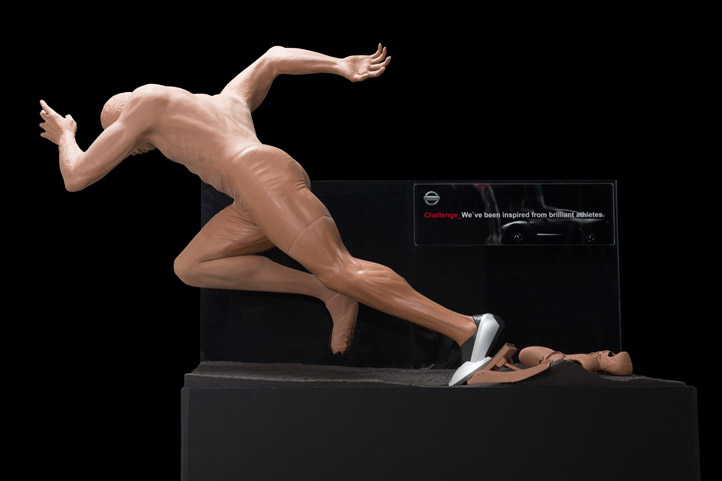
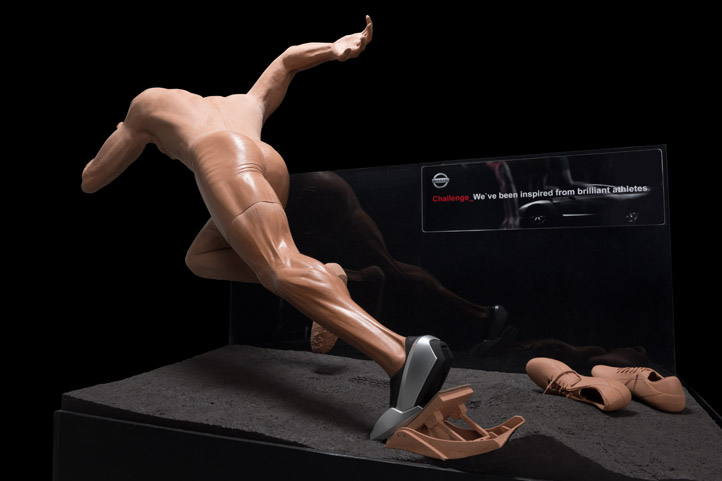
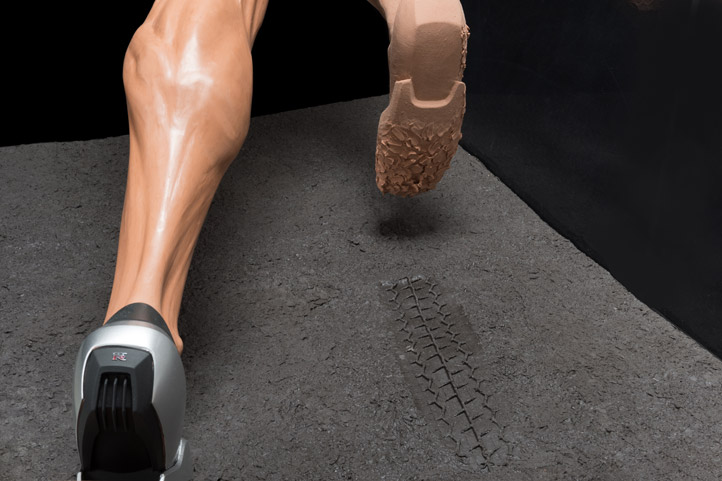
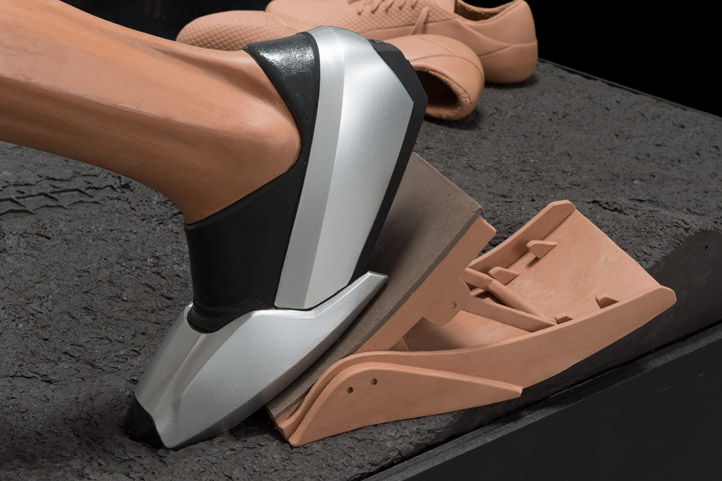
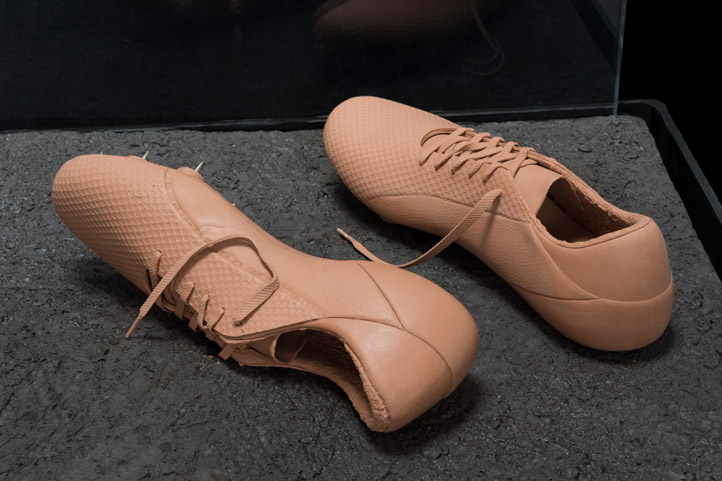
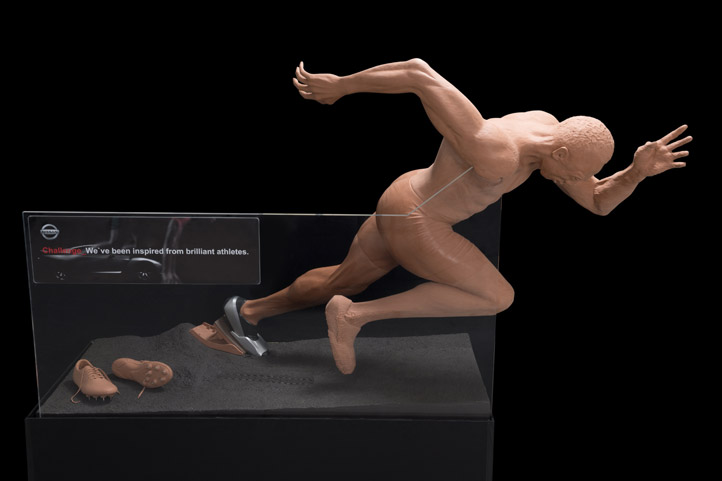
Carefully Studying an Object to Re-create It
The theme these creators chose for their clay model was “challenge.” Takumi Project leader Haruo Yuuki explains: “As clay modelers, we're constantly challenging ourselves to take our techniques to the next level. We saw parallels between this and the image of an athlete taking on the challenge of breaking a record.”
The project is unlike their ordinary workflow: they have no designers' sketches, which usually provide the basis for their creative efforts. “The group members did a thorough study of how a sprinter's muscles move by examining photos and videos of runners. Then we did our own sketches and worked to produce a common image to shoot for,” says Yuuki. “What we were aiming to express was the instant just when a sprinter takes off: the balance of his bone structure, the muscles carrying maximum energy, the taut connections between his tendons and muscles, and the entire overpowering aura of tension that an athlete projects.”
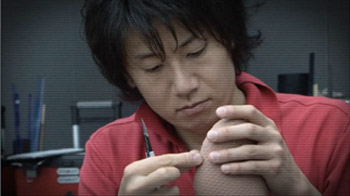
The modelers' task began with the creation of a smaller model, just 1/4 the scale of the final one. At this stage they worked on the model's overall composition, bearing in mind an image of how the final piece would look. This was followed by careful measurement of the dimensions of the smaller model, the design of the metal frame to support the larger piece, and finally the creation of that piece itself.
Here a question cropped up: how to achieve a balanced center of gravity in the form of an athlete leaning deeply forward. Visible support elements would wreck the visual impact of the model. The team discussed their options and decided to use a 20-millimeter-thick transparent acrylic plate, thus reducing the support's visible presence in the design. In the end, they accomplished a design whose implementation would astonish the people who did notice the support element.
Creativity Born from the Spirit of Challenge
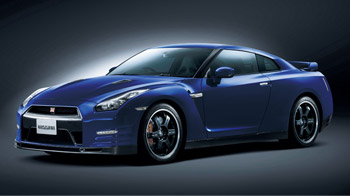
Once it was time to begin creating the full-scale model, Yukihiro Mae—a young modeler with Nissan for just nine years—became the team's leader. By tapping younger members to fill key posts, the Takumi Project plays an important role going beyond simply enhancing their technical skills: it trains them as successors to Nissan's leading employees today.
“In the full-scale model we sought to create a real sense of motion, not a stationary image. We used the contrast between roughly and finely finished areas to bring a dramatic energy to the piece,” Mae notes. While the team worked on the model, one of its members came up with the idea of using the form of Nissan's GT-R supercar in the sprinter's shoes. This would be an expression of the world's fastest athlete, exploding out of the blocks in GT-Rs transformed into track spikes. The youngest participant, Takamasa Ishimaru, talks about what he took away from the project: “We were able to flex our creative muscles?not just making an object, but creating it with proper consideration for all the concepts underlying it.”
The full-scale model took shape over a period of around a month. “The slightest loss of balance in a model of the human body can make it no longer look like a person. This task confronted us with difficulties we don't experience when we create manufactured goods,” reminisced Mae after the project's end. “Nissan's clay modelers keep the spirit of challenge alive at all times. If you don't have that spirit—if you don't push yourself to take on difficult challenges—you can't create anything new. I think we poured as much as we could of this spirit of challenge into our clay model.
Challenge is more than just the theme of this Takumi Project session. It is a theme infusing the activities of these modelers each day as they pursue the essence of Nissan in their creations.