スーパーの食品売り場で美味しそうなイチゴを目にする季節になりましたね。カフェやレストランでもイチゴをメインとしたデザートが増えてきました。「とちおとめ」や「あまおう」といったおなじみの品種をはじめ、日本にはたくさんのイチゴの品種やブランドがあります。その一つが「食べる宝石」をコンセプトとした「ミガキイチゴ」です。
きれいなルビーレッドで形も美しい大粒なミガキイチゴは、有名百貨店では1粒1,000円で販売されることもある高級ブランドです。
このブランドイチゴの舞台裏で日産の工場でのノウハウがお役に立てるかも、ということをご存知でしょうか?
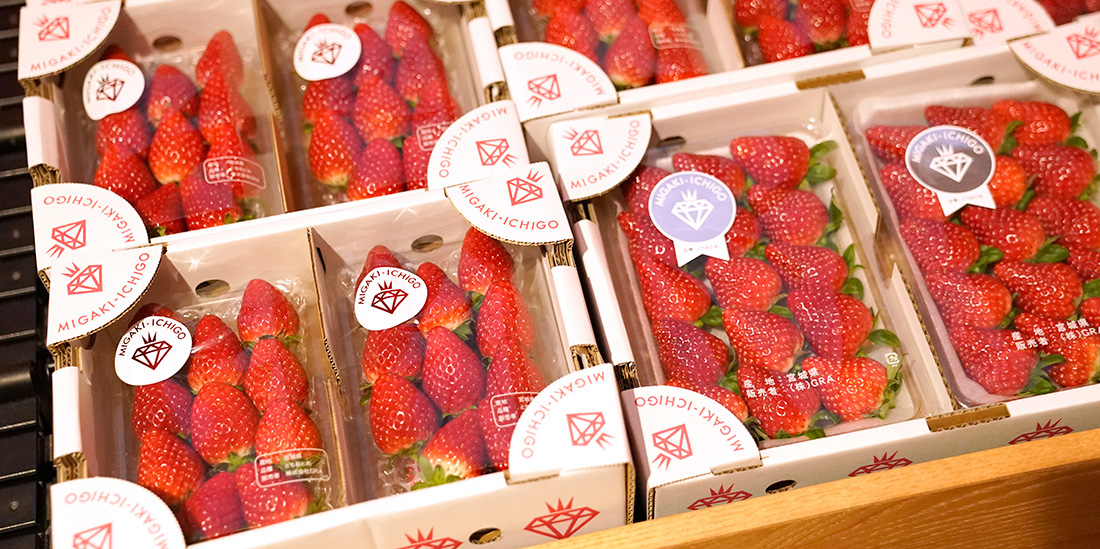
慎重さを求められる収穫
ミガキイチゴは品質にこだわり一貫して製造から販売まで行うことによって、ブランド価値を上げていき、他のイチゴと差別化を図ってきました。例えば、一般的なイチゴは60%程度赤くなったタイミングで収穫されるのに対し、ミガキイチゴの場合は90%くらいまで赤くなるのを待ってから収穫し、しっかりと熟した状態で出荷されます。イチゴは赤くなればなるほど柔らかくなり表面は傷つきやすくなるので、とても手間暇がかかるとともに慎重な作業が求められます。
ミガキイチゴを生産する農業生産法人 株式会社GRAで経営管理部門責任者の執行役員 上田 貴史さんによると、「どんどん赤くしていくと、どんどん柔らかくなっていくので、神経を注ぎますし、パックに詰めるパッキングであっても普段よりも一層神経を使います。輸送時にも傷んでしまうなど、ダメージを受けやすくなってしまいます」と話します。
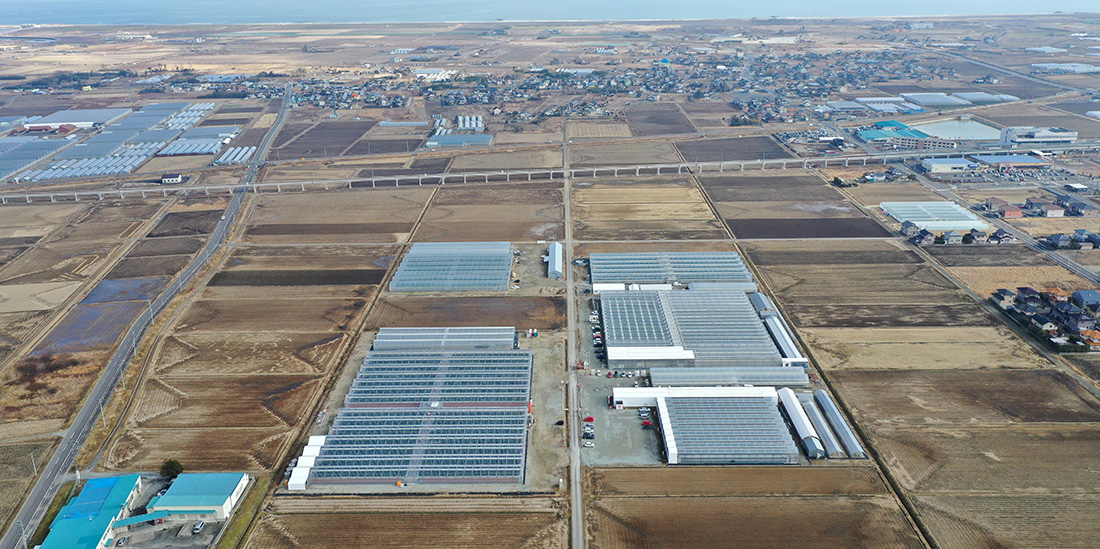
震災復興をテーマに掲げ
東北エリア随一ともいえるイチゴの産地・山元町には129軒のイチゴ農家がありましたが、2011年の東日本大震災の影響で、その内の122軒が津波で流されてしまいました。山元町出身の岩佐社長が、「壊滅状態となってしまったイチゴを栽培して地域の復興につなげたい」という思いで設立されたのがGRAです。GRAは、これまでのイチゴ栽培の職人が持つ長年の経験や知見といった伝統と、最先端の技術を融合した新しい“IT農法”に取り組んでいます。「ここでビジネスをもう一度起こし、人に来てもらい、雇用を増やし、ビジネスとして成功し、また産業として成り立たせることをGRAは目指しています」と上田さんは話します。GRAではイチゴの品質を維持しながら業務の負担を軽減し、生産性や効率を高めるために様々な取り組みを進めていたところ、ある農業の展示会で出展していた日産コンサルティングを知り、日産に生産工程の改善を依頼しました。
「日産が製造業で培ったノウハウを他の産業でも活かす取り組みを行っていると聞いて、是非ともお願いしたいと思ったのがきっかけです。」
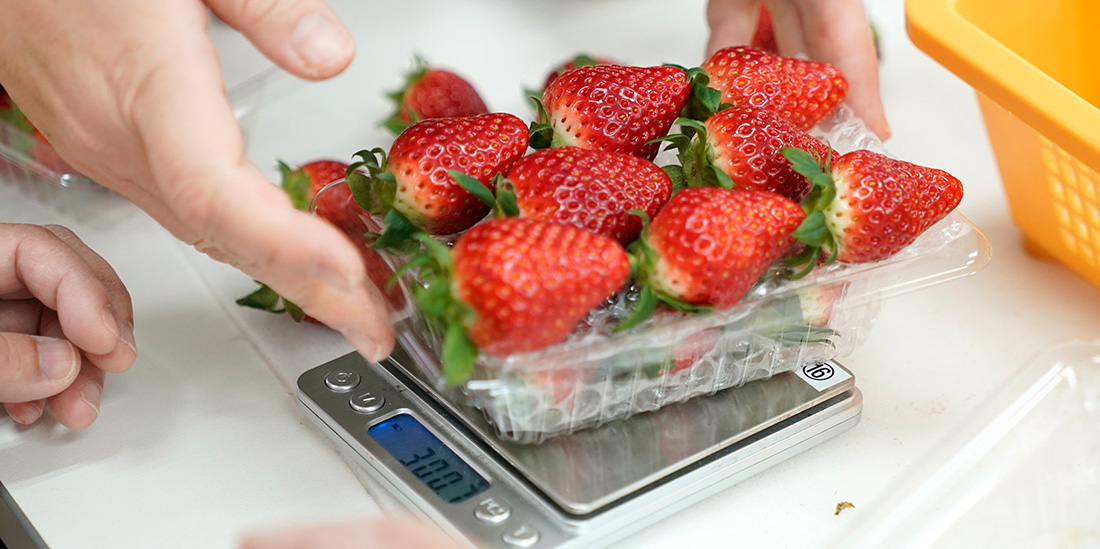
ローテクとハイテクによる改善
日産はローテクとハイテク、2つの異なるアプローチで改善プランを提案しました。
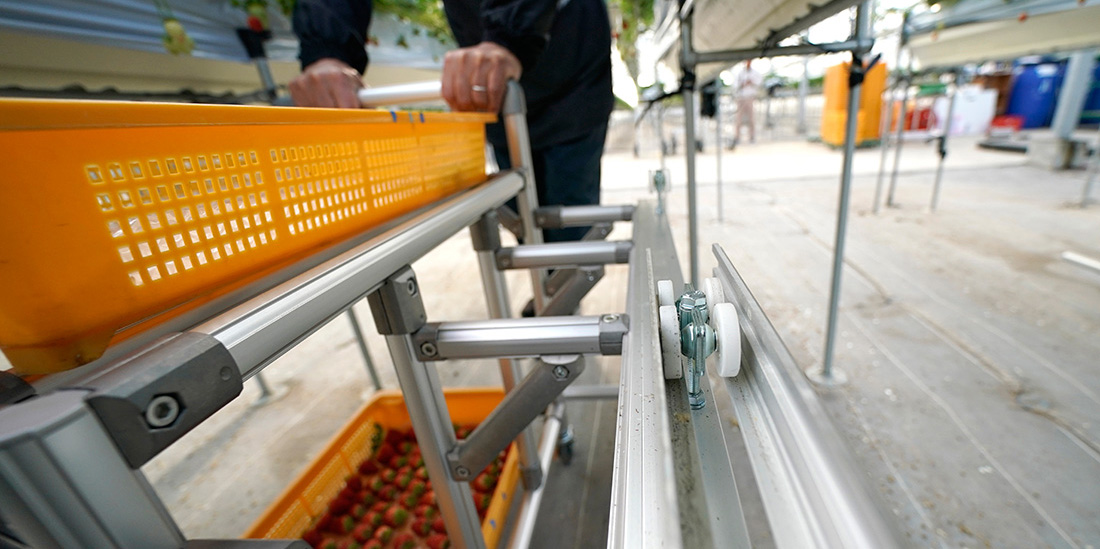
一つ目はローテクな改善プラン。面積を合計するとおよそ28,000m2にもなる広大なイチゴハウスで、収穫者がトレイを持ち歩きながら丁寧に収穫すると、手間暇と肉体的な負担がかかります。台車を使用して収穫をすれば効率は良くなりますが、地面が凸凹なため振動が起こることでイチゴを傷めてしまい、実用的ではありませんでした。そこで、これまで日産の工場で作られたいくつもの「からくり」の経験をもとに、台車の改善に取り組みました。(からくりとは、電気やコンピューターを使うのではなく、テコの原理や重力などを活用した機械的な装置のことです。関連ストーリーズはこちらから)
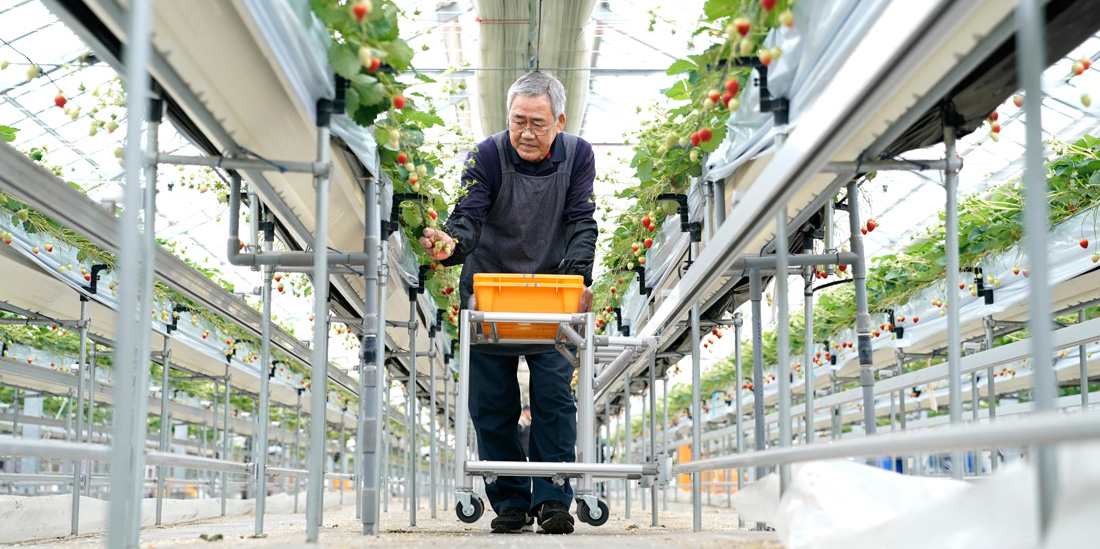
日産は、トレイを載せたアルミ製の台車の横に滑車を取りつけて、モノレールのように進む仕組みを考案しました。台車は地面から浮くので振動は無くなり、イチゴが傷むことはなくなります。また複数のトレイを運べるので、トレイがイチゴでいっぱいになっても空のトレイと交換する手間が省けることで効率性が大幅にアップします。これまで、摘んだイチゴでいっぱいになると重さ2キロにもなるトレイを持って、1日に2~4kmほど歩いていた収穫者の負担は大幅に軽減されました。
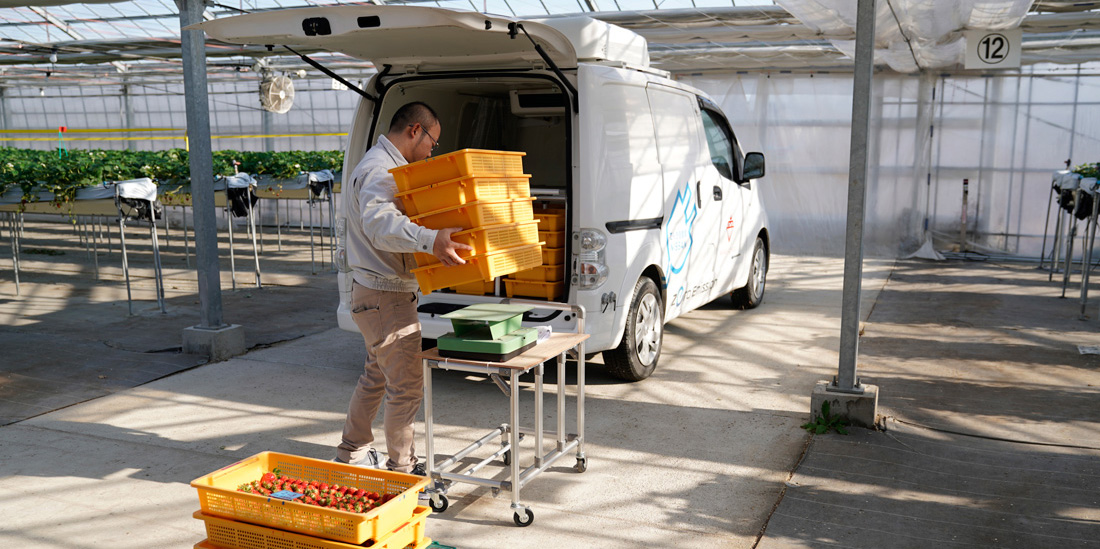
鮮度の維持は低温保存がカギ
二つ目はハイテクな改善。イチゴがベストな状態は摘んだ直後です。イチゴは柔らかいため、なるべく温度を下げて扱ったほうが傷みづらくなります。そのベストな状態を保つためには、収穫した直後から選果しパックに詰めて出荷するまで、ずっと冷蔵する必要がありました。しかし収穫してから選果する場所へ運ぶ間、低温を維持することができませんでした。そこで日産は「e-NV200」の冷蔵仕様車の導入を提案しました。「e-NV200」は「日産リーフ」のテクノロジーをベースにしたゼロ・エミッションのバンです。
これまで使用していたガソリン車では、排ガスが出るために密閉されたハウス内に車両を入れることができませんでした。一方「e-NV200」は排気ガスを出さないので、車両をハウス内に入れて作業を行うことができます。収穫した直後からお店に届けるまで温度変化することなく冷蔵保存できるので、鮮度が長持ちすると同時に傷むことがありません。「e-NV200」の導入は、収穫から店頭に運ぶまでの「コールド」を実現させました。
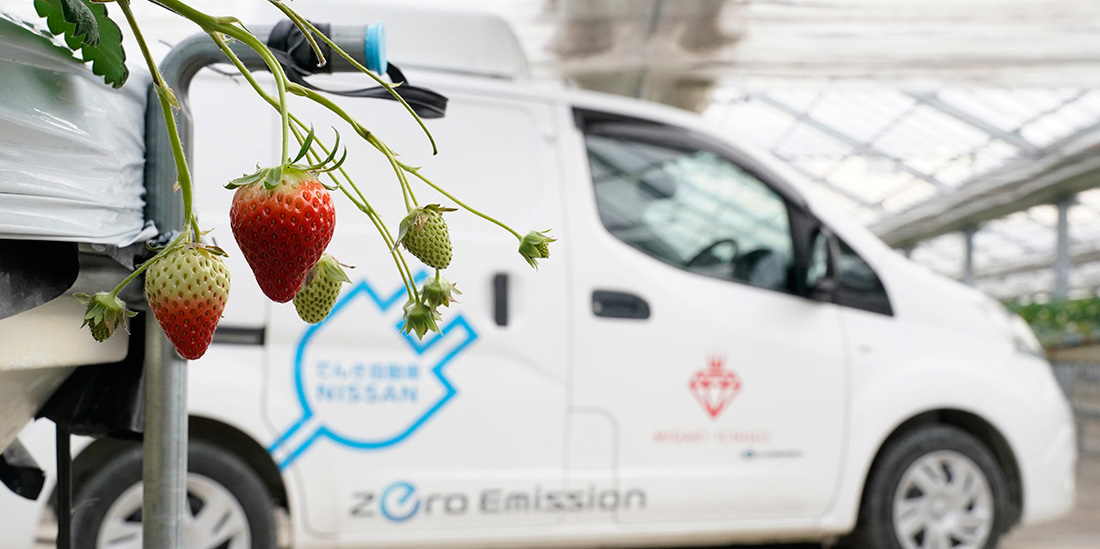
GRAが取り組む伝統と先進技術を融合したIT農法に、日産が自動車製造業で培ったノウハウをベースにしたハイテク/ローテク改善プランは見事にフィットしました。この活動は2021年3月まで継続し、活動結果の振り返りを実施したうえで取り組みを拡大する予定です。
最後に上田さんは、「より改善をして、より我々自身が農業から製造業へ近づくことができれば、日産さんからのアドバイスを引き続きもらいながら協力していただきたいと思っています」と今後を見据えています。
日産の生産方式「アライアンス・プロダクション・ウェイ(APW)」のコンサルティングを担当する瀬戸口 慎は「これからも農業に限らず、幅広い業種、業態、業界と一緒になって活動することで、わたしたちも知見をいただきたいですし、日産のノウハウもいろんな方に使っていただいて、喜んでほしいなと考えております」と語りました。
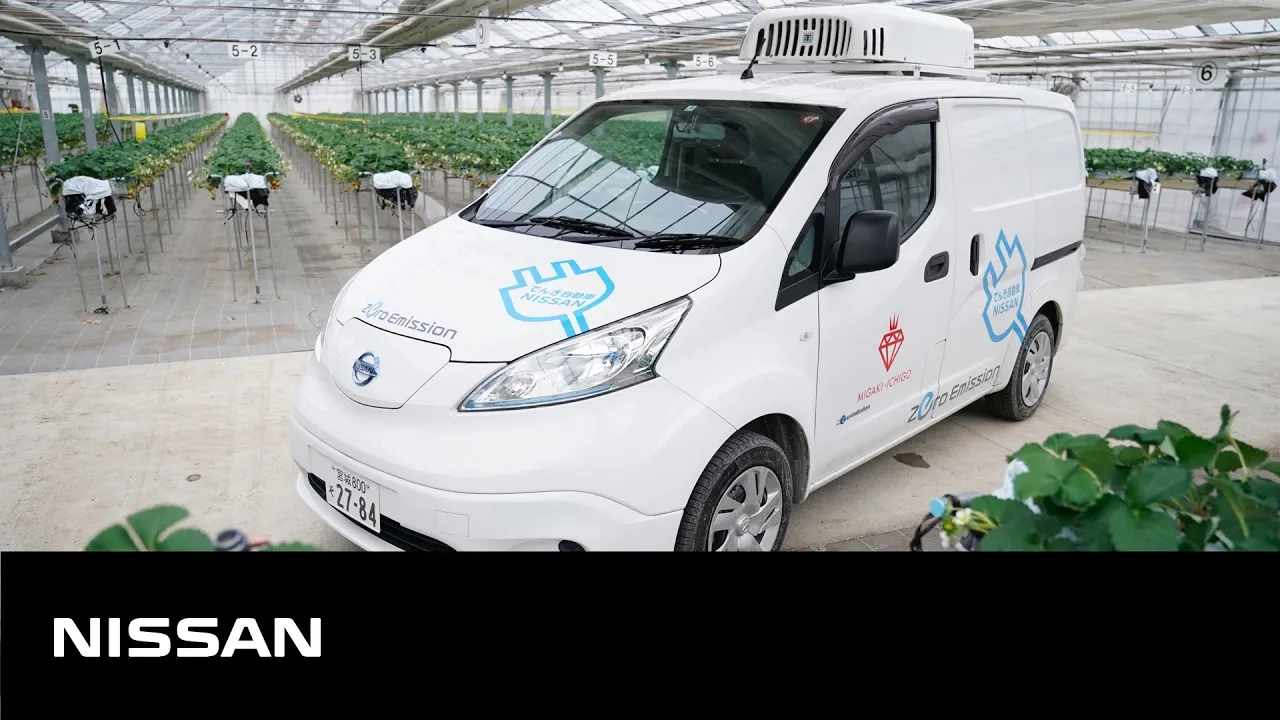